Exactly how to Recognize What is Porosity in Welding and Improve Your Technique
Wiki Article
Porosity in Welding: Identifying Common Issues and Implementing Ideal Practices for Prevention
Porosity in welding is a pervasive problem that often goes undetected till it triggers substantial issues with the honesty of welds. This common flaw can compromise the stamina and durability of bonded frameworks, positioning safety and security risks and resulting in pricey rework. By understanding the origin of porosity and executing efficient avoidance strategies, welders can substantially boost the quality and dependability of their welds. In this conversation, we will certainly explore the essential aspects adding to porosity development, analyze its harmful results on weld efficiency, and talk about the most effective practices that can be embraced to reduce porosity incident in welding procedures.Usual Reasons For Porosity
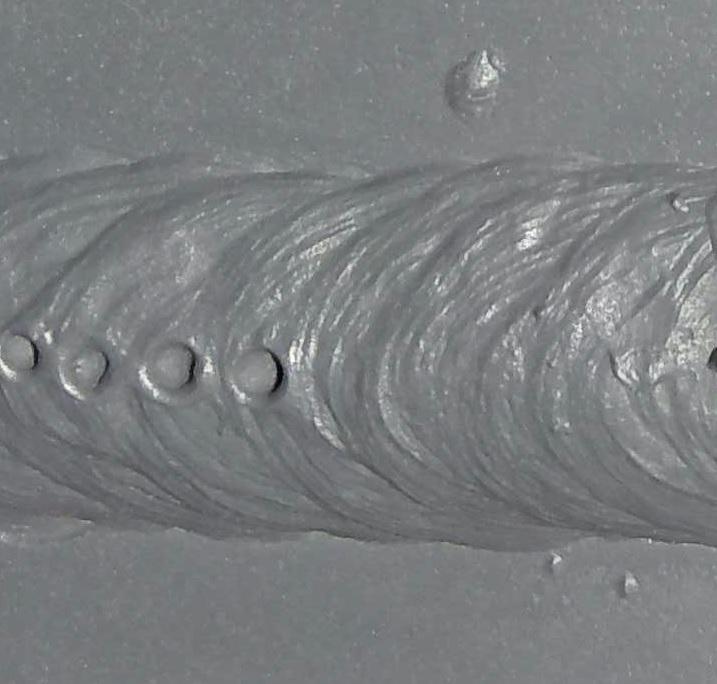
An additional frequent perpetrator behind porosity is the presence of pollutants externally of the base metal, such as oil, grease, or corrosion. When these contaminants are not successfully gotten rid of before welding, they can vaporize and end up being entraped in the weld, causing flaws. Furthermore, utilizing filthy or damp filler products can introduce pollutants right into the weld, adding to porosity issues. To minimize these usual reasons of porosity, extensive cleansing of base steels, correct securing gas option, and adherence to optimal welding parameters are vital methods in accomplishing high-grade, porosity-free welds.
Influence of Porosity on Weld Top Quality

The visibility of porosity in welding can dramatically endanger the structural integrity and mechanical homes of welded joints. Porosity develops spaces within the weld metal, weakening its total stamina and load-bearing ability. These spaces function as stress and anxiety focus points, making the weld more at risk to fracturing and failure under used tons. Additionally, porosity can lower the weld's resistance to deterioration and other ecological elements, further lessening its durability and efficiency.
Welds with high porosity levels have a tendency to display lower effect stamina and minimized capability to warp plastically prior to fracturing. Porosity can hamper the weld's capability to successfully transfer pressures, leading to premature weld website link failure and potential safety hazards in crucial structures.
Best Practices for Porosity Avoidance
To boost the architectural honesty and high quality of welded joints, what particular steps can be implemented to minimize the event of porosity throughout the welding process? Porosity prevention in welding is crucial to guarantee the honesty and stamina of the final weld. One reliable technique appertains cleaning of the base steel, getting rid of any type of contaminants such as corrosion, oil, paint, or wetness that could lead to gas entrapment. Making certain that the welding tools is in excellent problem, with clean consumables and ideal gas flow prices, can likewise considerably reduce porosity. In addition, maintaining a secure arc and managing the welding parameters, such as voltage, present, and travel rate, helps develop a consistent weld swimming pool that reduces the threat of gas entrapment. Using the proper welding method for the details material being bonded, such as adjusting the welding angle and weapon placement, can additionally prevent porosity. Routine examination of welds and instant removal of any problems recognized during the welding process are crucial methods to stop porosity and produce high-grade welds.Relevance of Correct Welding Strategies
Carrying out proper welding methods is critical in making certain the structural integrity and high quality of welded joints, developing upon the foundation of efficient porosity avoidance steps. Too much warm can lead to raised porosity due to the entrapment of gases in the weld pool. In addition, using the proper welding parameters, such as voltage, present, and take a trip speed, is vital for achieving sound welds with marginal porosity.Additionally, the option of welding procedure, whether it be MIG, TIG, or stick welding, ought to line up with the details requirements of the job to make certain optimal results. Correct cleansing and view preparation of the base metal, in addition to picking the right filler material, are likewise crucial components of skilled official source welding methods. By sticking to these ideal practices, welders can lessen the danger of porosity development and create high-quality, structurally sound welds.

Checking and Top Quality Control Procedures
Evaluating procedures are crucial to find and stop porosity in welding, guaranteeing the toughness and toughness of the final item. Non-destructive testing approaches such as ultrasonic screening, radiographic testing, and aesthetic inspection are generally utilized to recognize prospective defects like porosity.Post-weld inspections, on the other hand, assess the last weld for any defects, including porosity, and validate that it fulfills specified criteria. Executing an extensive high quality control plan that consists of extensive screening treatments and assessments is paramount to reducing porosity problems and making certain the general top quality of welded joints.
Final Thought
In final thought, porosity in welding can be an usual problem that influences the top quality of welds. By identifying the usual reasons for porosity and carrying out best practices for avoidance, such as appropriate welding techniques and screening procedures, welders can guarantee premium quality and reliable welds. It is vital to focus on prevention approaches to reduce the event of porosity and preserve the integrity of bonded structures.Report this wiki page